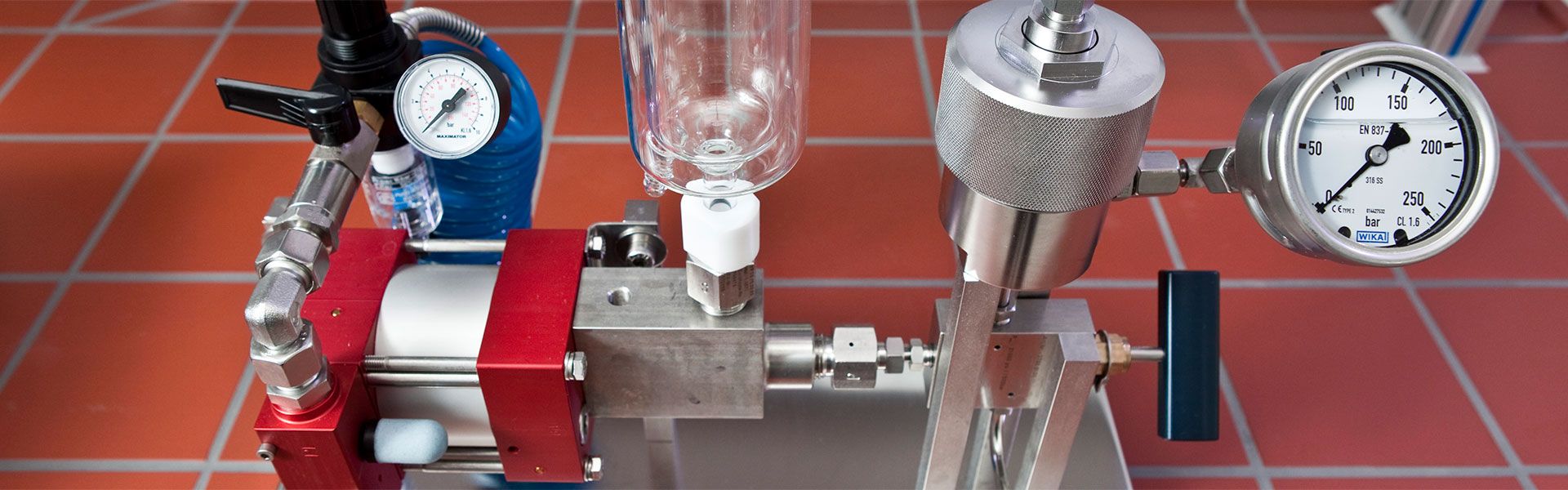
Maximator® high pressure extruder
This continuous high pressure extruder (HPE) allows rapid and reproducible large-scale production of unilamellar liposomes by filter extrusion over polycarbonate membranes.
Introduction
Due to its ease, reproducibility and flexibility filter extrusion has become the method of choice for the production of well-defined liposomes over a broad size range. However, since currently available pneumatic extruders (e. g. Lipex™ EXTRUDERS (NOTHERN LIPIDS), LiposoFast™ extruder (Avestin)) have limited maximum extrusion pressures and thus product flows the extrusion method seemed to be confined to lower lipid concentrations and smaller batch sizes.
With the introduction of continuous high pressure extrusion the limitations of discontinuous pneumatic extrusion have been overcome (US Patent 6,241,967). Thus, the Maximator® high pressure extruder model HPE 12.0 - 100 allows continuous production of liposomes at extrusion pressures up to 12.0 MPa (120 bar or 1800 psi). This extruder which employs a 47 mm filter holder has been designed for the production of liposome batches between 100 ml and approximately 3 liters as required for initial formulation development and (pre-) clinical testing. Depending on the employed filter pore size, lipid composition and concentration product flows up to 1100 ml/min can be achieved. Under identical processing conditions continuous high pressure extrusion resulted in factor 3.5 (5.0 µm) or 8.2 (0.05 µm) higher product flows compared to discontinuous pneumatic extrusion which resulted in a much shorter processing time (Berger 2001). Various bilayer components, including saturated and unsaturated phospholipids, cholesterol and charged lipids can be extruded at lipid concentrations up to 400 mg/ml without congestion of membranes. This process can potentially be scaled-up to any desired level by using larger pumps and additional filter holders if needed.
Function of the Maximator® high pressure extruder:
The Maximator® (Fig. 1) consists of a thermostatable glass supply vessel (1) directly connected to a pneumatic high pressure piston pump (2). The latter is driven by either oxygen or nitrogen at pressures below 0.5 MPa (5 bar or 75 psi). The propellant gas does not come into contact with the liposome suspension. The resulting operating (extrusion) pressure - which can be adjusted via the reduction valve in the control device for the propellant gas (3) - can be as high as 12 MPa (120 bar or 1800 psi) with the current equipment. The outlet side of the pump is connected to a filter holder (5) via a 3-way vent (4).
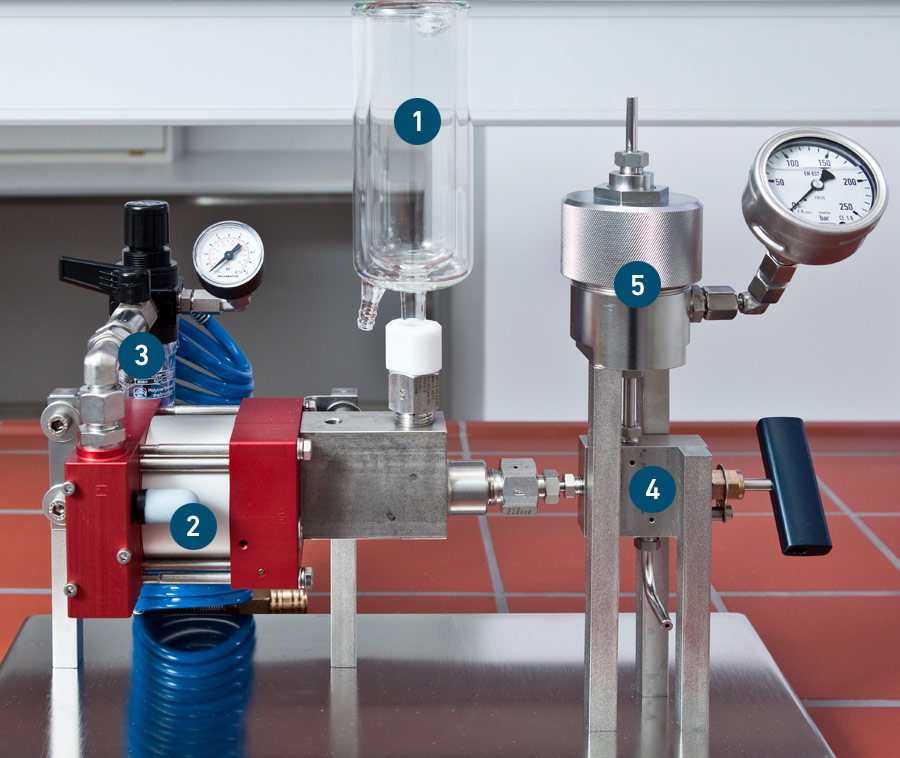
Fig. 1: Maximator® model HPE 12.0 - 100, continuous high pressure extruder. Extrusion with this apparatus is performed by introduction of MLVs into the supply vessel. The high pressure piston pump will pressurize the liposome suspension in the pump head and finally force it through the membranes in the filter holder. Typically sequential extrusion through two double stacked (sandwiched) membranes of decreasing pore size (e. g. 1.0, 0.2 and 0.05 µm) is performed. Normally, polycarbonate membranes (e. g. Nucleopore™) with pore sizes between 5 and 0.03 µm are used. In Fig. 2 the impact of the employed filter pore size on the size of the resulting liposomes is shown. The extruded vesicles can either be directly recirculated into the supply vessel to achieve automatic continuous extrusion or first be collected in a separate vessel to determine an exact number of filter passages. More details on the continuous high pressure extrusion process can be found in the papers provided in the reference list (e. g. Schneider 1994 + 1995, Berger 2001).
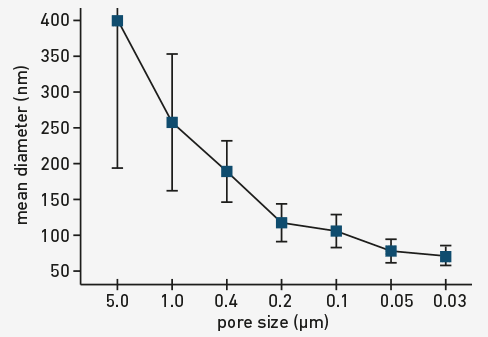
Fig. 2: Mean diameter of continuously extruded liposomes as a function of filter pore size (Schneider 1994)
Lipid composition: SPC/CH/SPG (6:3:1), 50 mg/g lipid, 100 ml batch (n=1)
Available models
There are three models of the Maximator® high pressure extruder:
HPE 12.0 – 100 (0.1 – 3 liter), HPE 12.0 – 1000 CE (10 - 50 liter)
and HPE 12.0 – 50 CE (0.05 – 1.5 liter).
Maximator® high pressure extruders for larger batch sizes are available upon request.
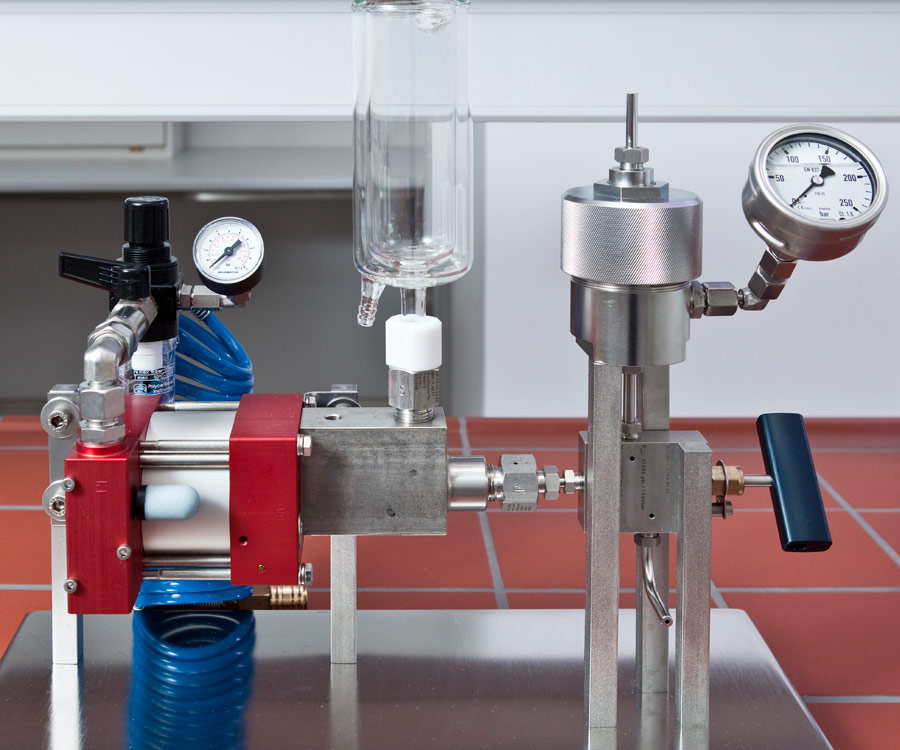
Model HPE 12.0 - 100
Standard small-scale continuous high pressure extruder for production of liposome batches between approximately 0.1 – 3 liter. The basic model comes without CE certification and does not require any electricity for use. Alternatively, a CE certified version is available (i.e. Model HPE 12.0 – 100 CE) which is additionally equipped with an emergency stop switch which requires electricity.
Special features of the Maximator® HPE 12.0 - 100:
- Simple recirculation without opening of a pressure chamber
- Fast exchange of membranes for sequential extrusion
- Ability to control product temperature
- Applicable for the generation of sterile preparations
- Easy to clean without need for disassembly (except for filter holder)
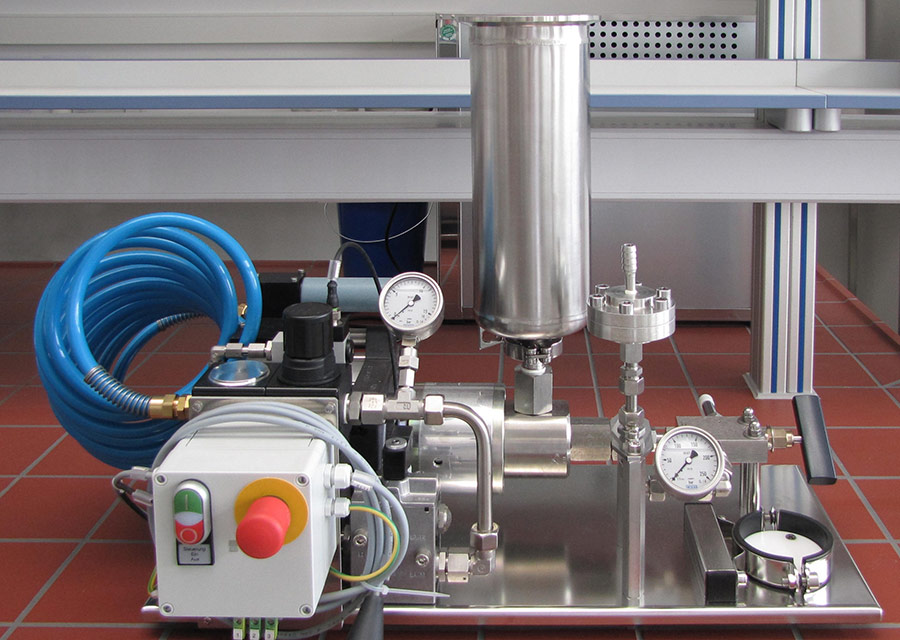
Model HPE 12.0 – 1000 CE
Large-scale continuous high pressure extruder equipped with an emergency stop switch for the production of liposome batches between approximately 10 and 50 liter. This extruder is routinely equipped with an emergency stop switch so that it always comes with CE certification.
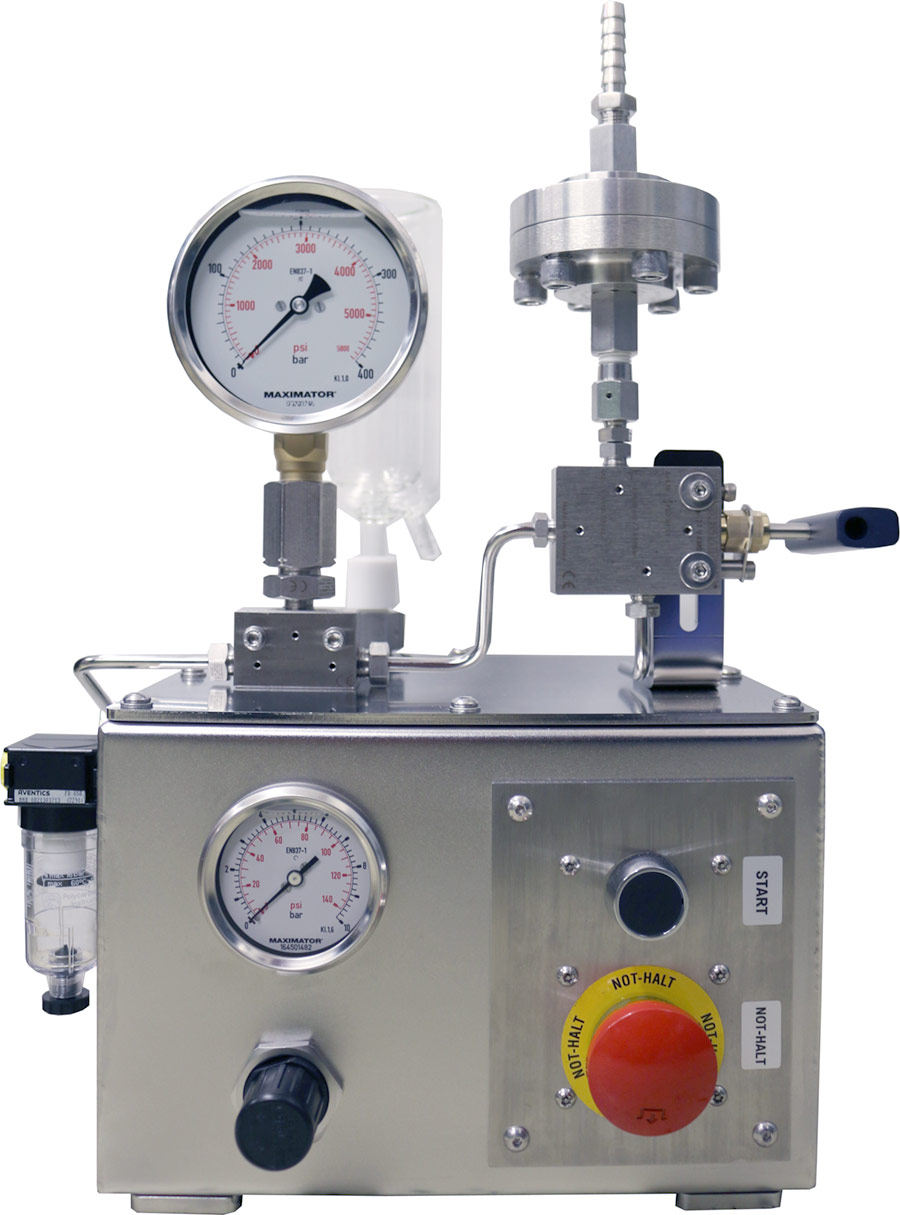
Model HPE 12.0 – 50 CE
Compact small-scale continuous high pressure extruder for production of liposome batches between approximately 0.05 – 1.5 liter. This model is equipped with a pneumatic emergency stop switch so that it does not require electricity for use.
Full operating instructions are supplied with each unit which need to be carefully read before first use of the Maximator® high pressure extruder.
Please contact CPL SACHSE for further information on our Maximator® product line or on high pressure extrusion for specific applications.
Note: The Maximator® high pressure extruders have formerly been distributed by DISPEX Disperse Systeme GmbH, Berlin, Germany.
FAQ
What is required for installation of the Maximator HPE?
The device comes as a ready-to-use unit which only has to be connected to compressed air or nitrogen via the polymer hose included in the delivery (via plug-in nipple).
Is electricity required to operate the Maximator HPE?
The standard unit (HPE 12.0 - 100) does not use any electricity unless you choose to supply the compressed
gas needed to drive the pump via an air compressor which is not part of the unit.
However, if CE certification is required an emergency stop switch which requires electricity has to be added
due to European regulations (model HPE 12.0 - 100 CE).
How is the propellant gas supplied to drive the high-pressure pump in the Maximator HPE?
Typically air or nitrogen from gas bottles or standard gas lines as available in most labs is used to drive the pump. The required working (i.e. propellant gas) pressure is obtained by adjusting the reduction valve in the control device of the unit.
What documentation is provided along with the Maximator HPE?
The unit is delivered with a comprehensive instruction manual, technical drawings (without dimensions) and parts list.
What kind of certificates are provided along with the Maximator HPE?
The model HPE 12.0 - 100 CE comes with an EC Declaration of the manufacturer according to the EC Machinery Directive 2006/42/EC or a declaration of incorporation in case of the standard model HPE 12.0 - 100.
What is the minimum liposome batch size which can be extruded with the Maximator HPE 12.0 - 100?
Due to the void volume of the unit as well as product losses which result when using different filter stages (i.e. pore sizes) for sequential extrusion the minimum recommended batch size is approximately 50 - 75 ml.
What is the maximum liposome batch size which can be extruded with the Maximator HPE 12.0 - 100?
The unit was originally designed for the production of liposomes up to the liter scale (0.1 - 3.0 liter) which should be sufficient for formulation development and initial (pre-) clinical testing. However, some clients routinely use the Maximator HPE 12.0 - 100 for the production of batches > 10 liters especially when only a single extrusion step (i.e. filter pore size) is required.
What are the maximum product flows which can be achieved with the Maximator HPE 12.0 - 100?
The product flow is dependent on the capacity of the propellant gas source, the required operating pressure and product characteristics.
What ist the highest operating (i.e. extrusion) pressure that can be used with the Maximator HPE 12.0 - 100?
The required/resulting operating pressure is a function of formulation properties and filter pore sizes. The unit allows extrusion of extremely concentrated and viscous preparations at pressures up to 120 bar if needed, but can of course be used at any pressure below the maximum as required (see also next question).
What ist the lowest operating pressure that can be used with the Maximator HPE 12.0 - 100?
As a rule of thumb x bar inlet pressure (i.e. working or propellant gas pressure) will result in x times 46 bar operating pressure due to the pressure ratio (approximately 1:46) of the employed high pressure piston pump. Therefore, the lowest extrusion pressure one can theoretically use is approximately 4.6 bar which is obtained when the working pressure (i.e. propellant gas) is adjusted to 0.1 bar by the reduction valve of the control device.
Does the Maximator HPE require any routine maintenance?
No special maintenance is needed. General maintenance instructions are included in the standard instruction manual.
Are there any wearing parts in the Maximator HPE which need to be exchanged on a frequent basis?
Except for the seals in the high-pressure pump the Maximator high pressure extruder does not have any wearing parts which need to be exchanged. Typically the seals last for several years.
Is a test device available which can be provided for initial testing?
We do not routinely provide our Maximator HPE for external testing. However, we offer to process test suspensions (preferably placebo preparations) provided by you with our in-house test device according to your extrusion protocol and to provide the respective samples and results to you. Alternatively, someone from your team can visit us to perform such tests in our lab.
Do you have a Maximator HPE for the production of larger liposome batch sizes?
High pressure extruders for larger batch sizes are available upon request and have to be customized according to your specific requirements (e. g. DQ).
Do you have a Maximator HPE for the production of smaller liposome batch sizes?
Smaller units for the production of liposome batch sizes below 50 ml (= minimum recommended batch size for Maximator HPE 12.0 - 100) are not available due to technical/practical limitations.
References
- Schneider, T., Sachse, A., Rößling, G. and Brandl, M., Large-scale production of liposomes of defined size by a new continuous high pressure extrusion device. Drug Dev. Ind. Pharm. 20, 2787-2807 (1994).
- Schneider, T., Sachse, A., Rößling, G. and Brandl, M., Generation of contrast-carrying liposomes of defined size with a new continuous high pressure extrusion method. Int. J. Pharm. 117, 1-12 (1995).
- Muschick, P., Sachse, A., Leike, J., Wehrmann, D., Krause, W., Lipid dependent cardio-haemodynamic tolerability of liposomes in rats. J. Liposome Res. 5, 933-953 (1995)
- Schneider, T., Sachse, A., Leike, J., Rößling, G., Schmidtgen, M., Drechsler, M., Brandl, M., Surface modification of continuously extruded contrast-carrying liposomes: effect on their physical properties. Int. J. Pharm. 132, 9-21 (1996).
- Sachse, A., Leike, J.U., Schneider, T., Wagner, S.E., Rößling, G., Krause, W., Brandl, M., Biodistribution and computed tomography blood-pool imaging properties of polyethylene glycol-coated iopromide-carrying liposomes. Invest. Radiol. 32, 44-50 (1997).
- Berger, N., Sachse, A., Bender, J., Schubert, R., Brandl, M., Liposome preparation by continuous and discontinuous extrusion, comparison of process parameters and liposome characteristics, Proc. 2nd World Meeting on Pharmaceutics, Biopharmaceutics, Pharmaceutical Technology, APGI/APV Paris, 655 (1998).
- Reszka, R., Fichtner, I., Goan, S.-R., Rudolph, M., Winter, R., Encapsulation of the transition metal compounds carboplatin (CP) and lobaplatin (LP) in different types of liposomes and their physico-chemical, biochemical and biological characterization, in Bioinorganic Chemistry, Transition metals in biology and their coordination chemistry, (Trautwein, A. X., Ed.) Wiley-VCH, 145 (1998).
- Sachse, A., Large-scale production of liposomes by continuous high pressure extrusion, in R.H. Müller, S. Benita and B. Böhm (eds.), Emulsions and nanosuspensions for the formulation of poorly soluble drugs, Medpharm Scientific Publ. 257-265 (1998).
- Berger, N., Sachse, A., Bender, J., Schubert, R. and Brandl, M., Filter extrusion of liposomes using different devices: comparison of liposome size, encapsulation efficiency, and process characteristics, Int. J. Pharm. 223, 55-68 (2001) (Full text).